
How Are Rubber Products Used in Our Daily Lives?
We see, feel, and use rubber products now more than ever. Rubber is versatile, resilient, and durable. This makes it an ideal raw material for many products. Through rubber extrusion, rubber assumes the form you desire.
At Clark Rubber and Plastic, we create custom rubber extrusion products for different industries. Discover how our rubber manufacturing processes come in handy in your daily life.
Rubber Use for Appliances
Washing machines, microwaves, dryers, vacuum cleaners, and other home appliances use rubber components. We provide appliance companies with high-quality rubber parts for different products.
We understand the appliance industry’s need to use components that guarantee safety and reliability. At Clark Rubber and Plastic, we use advanced equipment to extrude rubber. We can meet your needs and specifications.
Applications for our rubber extrusion services include:
- Gaskets and seals to prevent leakage.
- Vibration elimination rubbers for washers/dryers.
- Water barriers for dishwashers and washing machines.
- Air sealing rubbers for freezers, refrigerators, and ovens.
Rubber Extrusion for Automotives
We manufacture automotive rubber parts. We offer rubber extrusions for different automotive products regardless of make, size, or shape. Clark Rubber and Plastic tailor products to meet your demands and needs.
Here is a list of car components we will tailor-make for you:
- Tires – Our tires are known for enduring extreme temperatures and retaining their shape while carrying heavy loads. We provide you with durability, good wet grip, and better handling from our rubber tires.
- Car Rubber Pads – We incorporate anti-slip designs into our pedal rubber pads to guarantee better foot control.
- Hoses – We make our car hoses, fuel, radiator, power steering, and heater, from high-quality rubber. Car hoses get exposed to extreme temperatures and harsh chemicals that can cause damage. Our hoses are ideal for your vehicles since they can withstand these extremities and are flexible.
- Seals – Our leaks will counter any leakages, noise, and vibrations. We have both crankshaft and radiator seals.
- O-Rings – These gaskets create an air-tight and liquid-tight seal to prevent oil from flowing into the combustion chamber.
- Grommets – These provide cushions for wires in holes throughout the vehicle.
- Bushings – Our car bushings prevent vibrations and reduce friction between your vehicle’s metallic surfaces.
- Mats – Rubber mats effectively protect your vehicle’s interior. Clark Rubber and Plastic specialize in producing up to standard car mats that can withstand wear and tear.
Rubber Use for Construction
The versatility and durability of rubber make it ideal for construction use. We create rubber extrusion in diverse profiles, shapes, forms, thicknesses, densities, and textures to meet your needs. Our extruded rubber withstands hot and cold extremities and is waterproof, mold-resistant, and rustproof.
Rubber Uses in the Solar Industry
At Clark Rubber and Plastic, we produce silicon rubber that is perfect for solar energy industries on large and small scales. Its host of features allows us to produce vacuum membranes for solar panels and wind turbine blades.
Purchase Rubber Extrusion Today
Our cutting-edge equipment gives us an upper hand in producing high-quality rubber for our clients. Rubber extrusion parts from Clark Rubber and Plastic give your products the touch they need
Contact Clark Rubber and Plastic today to purchase an appliance, automotive, construction, or solar rubber parts. Our specialists work with you to find the right products for you. Request a quote to get started today.
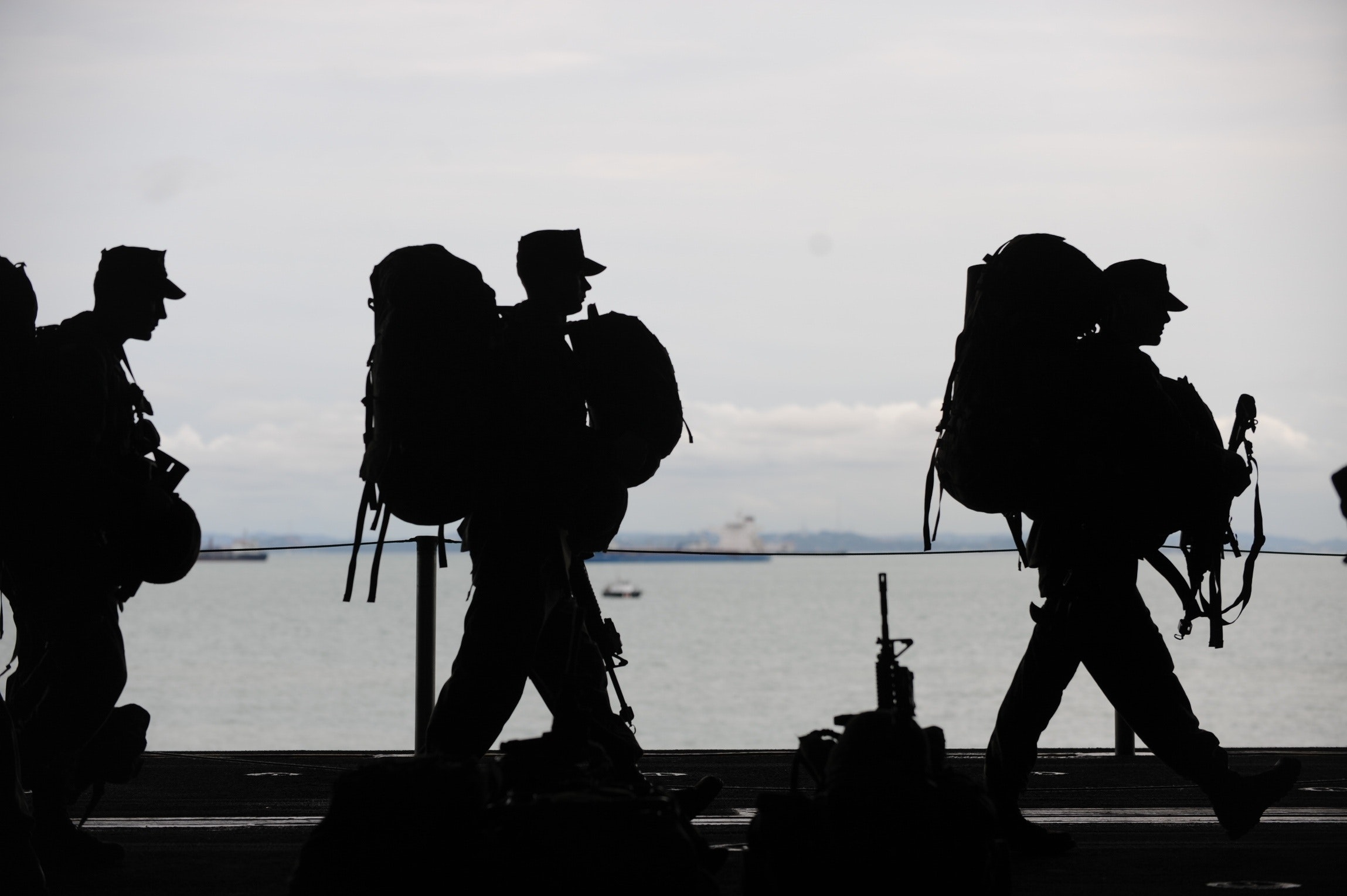
How Are Plastics for the Military Manufactured and Used?
At Clark Rubber and Plastics, we have a proud history of providing parts that can withstand high-stress scenarios. Our team knows plastics need to be of high standards to meet the strict needs of the military and defense industries. Our experience in constantly meeting these requirements makes us one of the top military parts manufacturers.
We strive to build long-term relationships with each client by working to know their needs. With a reliable partner, you can source parts from providers who’ll make and deliver them when you need them most.
Today, we’ll discuss the assembly process of military plastics. We’ll also talk about how the military industry uses plastics to help improve how they function.
The Assembly Process
The military builds its plastic products through a process called plasdtic injection molding. Here are the steps we follow to create a product:
- Build or choose a custom plastic mold
- Choose components to best address the project needs
- Inject the molten parts inside the mold
- Allow them to cool down
- Put together the end product
Depending on the design and parts, it can help a product withstand hot weather and vibrations. These products can also resist water and protect troops on the front lines from explosions and other dangers.
We perform the injection molding process with many types of materials, including:
- Confections
- Elastomer
- Glass
- Metals
- Polymer
Using plastic moldings instead of metal can save you significant amounts of money on equipment costs. They are also strong and durable, making them popular in a variety of industries.
5 Ways We Use Plastics To Improve Functionality
Plastics can provide you with many features that other types of parts can’t. At Clark Rubber and Plastics, we work with military parts manufacturers to make components that will last.
Here are some of the funcitonal benefits of our plastics:
1.) Lightweight Gear for Troops
Plastics can provide troops on the front lines with flexibility that other parts may not. They allow you to have the proper strength-to-weight ratio. Military plastics can be as durable as metals but will help reduce the weight of the equipment.
Tactical gears for troops need to be light enough for them to carry. They also need to have the strength to handle any scenarios while they’re on duty. With plastic materials, you can build gear that provides our troops with comfort and helps keep them safe.
2.) Short Manufacturing Lead Times
Using metals to build products requires a workshop to cast them into the right shape before even beginning production. Metal products will require long time frames to complete the whole process.
Plastic resins offer you short lead times to have your product ready when you need it. They only need a small amount of mixture and pellet formation. These processes will allow you to mold them into parts more quickly. You’ll also be able to have the final product ready to ship out on time to your clients.
3.) Improved Corrosion Resistance in Equipment
Jets and gears that contain metal can corrode slowly over time. By using plastic to build products, you can get around this issue.
You can also add UV stabilizers and other anti-corrosion parts into plastic resin before you mold the parts. With plastic elements, your equipment and combat vehicles will perform in optimal condition on the field or in the sky.
4.) Reliable, Precise Products
Many military apps need to have top precision to work in rapidly changing environments. Optical gear and small hand-held tools must have reliable and measurable preciseness to function at their best.
Plastics can provide you with that precision for the duration of the process. You won’t need to tweak the tools or minor components to build your products. Plastic parts won’t alter past their levels and will help you gain the best readings.
5.) Stealth-enhancing Product Features
Metal parts can leave large sonar or radar echo signs. They can also leave heat source footprints that other forces may see. Plastic resins can help you upgrade your stealth functions for military operations.
Here are some ways non-conducting resin can help strengthen your forces:
- Domes with polymer elements can shield detection tools and hide vibration on ships and planes.
- Military choppers with acoustic and infrared radar with polymer foam blades help you hide your position from the enemy.
- Polymer coating on military trucks can help you counter visual detection from enemy forces.
By staying undetected, your forces will gain the upper hand and stay safe while on the front lines.
Military Parts Manufacturers: Keeping Our Forces Strong
Our team has put together quality assurance systems that help products meet or exceed the safety goals of our clients. At Clark Rubber and Plastics, we have a track record of providing military and defense complexes with high-quality products and fast turnaround times. We also are flexible in helping you carry out short or full production runs in the moments that matter most.
Contact us today to learn more about our plastic manufacturing functions and how we can help you grow in your industry.
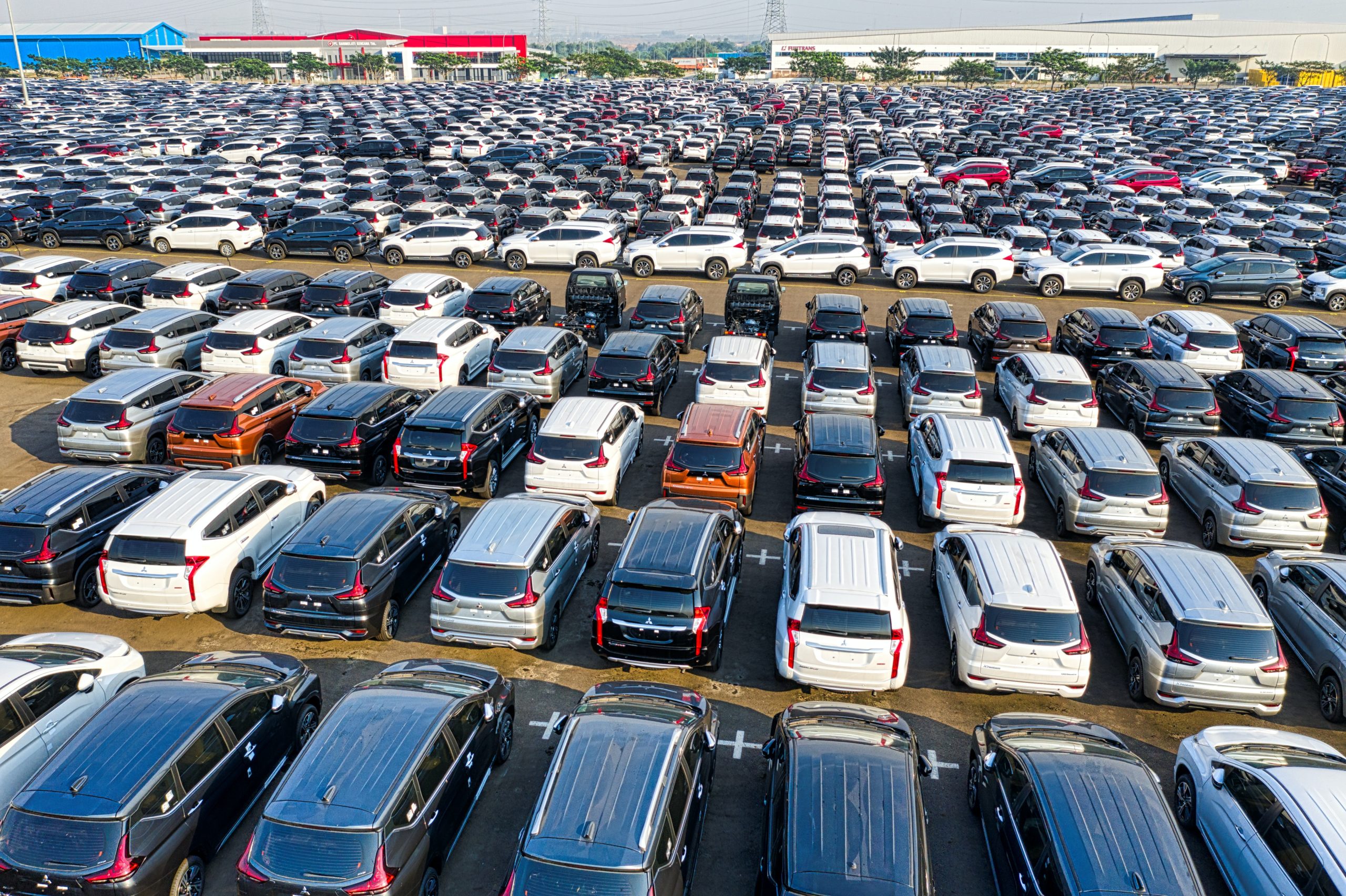
7 Ways The Automotive Industry Uses Plastics
At Clark Rubber and Plastics, we believe world-class automotive plastics help companies like yours have top-quality auto parts. Dependable auto parts can affect a car’s efficiency, while reliably built plastics can impact its performance. Our team has the tools to meet your needs and help you compete in your industry. With our skills and expertise, you can enhance the safety and performance of each car.
Here are seven ways the auto industry uses plastics to improve how they operate:
1) Plastics Have Lightweight Elements That Help Lead To Better Fuel Efficiency And Performance
Cars today contain 50% plastic by volume and are only 10% of a car’s total weight. Plastics can make a difference when you include them as part of a car. They have lightweight elements that help boost a car’s fuel efficiency. Lighter cars can also speed up faster when you press the pedal to the floor.
Electric cars with plastic material can provide you with a higher per-charge range. These elements allow you to avoid having to replace your battery with one of a bigger size.
With lightweight plastics, you’ll be on track towards building up the performance of each car you build.
2) Plastics Help Bring You Lower Car Assembly Costs
Many materials companies use to build cars can be costly. Automotive plastics can be an effective way to help you lower costs.
Single-mold parts lead to faster assembly times and allow you to add new innovative designs to each car. Plastics are also cheaper to make and fit than other materials, such as metal. When cars are more affordable to build, car companies can then pass those savings on to buyers.
For dents and scratches, plastic car door cladding and bumpers are easier to fix or replace than metals. By using plastics to assemble a car, the builder and buyer will gain more cost savings. You’ll also help your business be unique in the process.
3) Plastics Provide You And Your End Users With Greater Safety
Car safety features like seatbelts and airbags come from solid polyester substances. When a car accident occurs, these features and outer plastic parts like bumpers and car door cladding can handle impacts better than metal. These durable materials will help lead to safer outcomes for drivers and their cars.
Plastic fuel tanks also have some of the best safety features. Since car builders can make them as solo parts that don’t contain fused seams, no seams will fail during collisions.
Automotive plastics help strengthen the safety of each car when compared to metals. They also help drivers and guests feel more safe while on the road.
4) Plastics Can Withstand Harsh Weather And Glass Damage
Harsh weather conditions can have an impact on a car over time. You can reduce corrosion by adding a synthetic plastic coating to a car’s metal surface.
Here are three types of weather events in which coatings can protect a car:
- Excess heat
- Exposure to water
- Salt damage
Glass windshields with plastic film coats can also help improve their weather resistance and reduce wear and tear. They can even reduce the likelihood of chips forming on a windshield or glass shatterings. Coating or making your parts under the hood with plastics can provide resistance to abrasion and help vehicles be flexible.
As you add automotive plastics to your process, your cars will gain a longer lifespan.
5) Plastics Are More Eco-Friendly
Plastics usually are viewed as wasteful by those passionate about the environment. When it comes to car assembly, the reverse is true. Many auto companies use recycled plastics to build parts such as bumpers, seat cushions, splash guards, and wheel liners.
These products provide them with methods to merge parts from old cars to new ones and achieve eco-friendliness. Automotive plastics will also keep end-of-life cars from ending up in a landfill.
6) Plastics Help Bring Drivers And Their Guest The Best Comfort
Plastics made for cars can provide drivers and guests with a more comfortable commute. These materials are made for noise, vibration, and harshness (NVH) parts that help reduce a car’s sound and vibration while on the road. They also filter out harmful sun rays that prevent heating up too much during the summer.
As for drivers, the plastics will help them have a firmer grip on the wheel. Your end users will have the best driving experience possible with this material comprising important parts of their vehicle.
7) Plastics Have Good Thermal Insulation
During the car building process, car makers find spots where the engine heat impedes other areas of a car. Those hot spots can even get into a car’s interior. Eco-Fi felt material helps builders cover up those spots. Felt comes from recycled plastic bottles and provides each car with more than enough thermal insulation. With these reusable products, builders can cool down those hot spots and help protect drivers and their guests.
Choose An Automotive Plastics Provider That You Can Count On
Our tech tools allow us to build a range of automotive plastics that perform at a high level. At Clark Rubber and Plastics, we have a track record of providing businesses with short lead times and fast turnarounds. Our team is certified to provide you with the parts you need.
Contact us today to learn how our plastic extrusion services can help reshape your business.
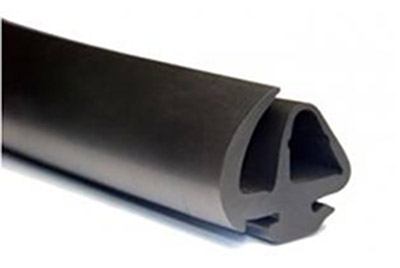
How Do Auto Manufacturers Use Rubber Molding?
Rubber is a popular material in modern automotive design and is used in different components. At Clark Rubber and Plastic, we offer rubber molding for brakes, transmission systems, engines, steering, ac, clutch assembly, solenoid valves, and more. Rubber components are lightweight and provide shock absorption found across the car. Here are four ways auto manufacturers use rubber:
1. For Bumpers & Bushes
Rubber bumpers and bushes offer shock absorption and can minimize the damage caused by a collision. Auto manufacturers use natural and synthetic rubber-like silicone, urethane, butyl, and polyurethane. Rubber bumpers come in various shapes and sizes and reduce vibration, movement, and impact. Bushings are used to absorb shock and provide spacing between parts.
Rubber bumpers and bushing offer sliding resistance and protect the surfaces from skidding and scratches. Other uses include vehicle cooling systems and heavy-duty dock applications. Clark Rubber and Plastic provide rubber parts in different colors, so you can find the perfect choice for each car. The products feature unique properties, including hardness and elasticity.
2. For Seals & Gaskets
Rubber seals and strips are common in car doors and windows. They’re used in various other parts to create a watertight seal, like in the case of O-rings. Rubber seals are waterproof and come in all shapes and sizes customized for the application. The material is resistant to abrasion and chemicals, making it perfect for different settings. Rubber is durable, flexible, and an efficient insulator.
We provide custom rubber seals for vehicular openings, including roof rails, cowl, window pillars, and divisions. Clark Rubber and Plastic manufactures premium quality rubber gaskets for car engines. Head and manifold gaskets prevent coolant, oil, and air leakage from the combustion chamber and gunk from the transmission.
3. For Engine Mounts & Housing
Rubber engine mounting is vital in isolating, absorbing, and reducing vibration. Car engines work at high speed with multiple moving parts that can cause shaking. Without rubber mounting, the vibration is transmitted to the car’s body and the passenger.
The vibrations can increase wear and tear, so rubber mounting and housing are beneficial for the vehicle’s function.
Our rubber motor housing and mounting dampen noise and vibration, balance energy absorption, and reduce downtime. The housing is resistant to various conditions, including high and low temperatures, acids, chemicals, flame, oil, water, weather, tear, and abrasion. We offer different types of rubber that last several years.
4. For Diaphragms & Hoses
Car diaphragms act as a barrier between chambers and can move up or down, depending on the pressure difference. Diaphragm pumps are standard in mechanical fuel pumps. Rubber is the perfect material for car engine diaphragms and can last several months or years. They are waterproof, durable, and efficient.
Nearly all hoses used in the car transmission system are made from rubber. The fuel and brake fluid feed hoses use rubber, which is efficient under high temperatures and chemicals. Rubber hoses are durable, flexible, and less vulnerable to cuts and abrasions. They supply water, oil, and other fluids to different parts of the car, including the engine, radiator, and brakes.
Dependable Rubber Molding for Cars
Are you looking for top-quality rubber molding for your customers? Clark Rubber and Plastic is an experienced manufacturer of rubber and plastics used in various industries, including automotive, solar, and appliances. We can provide custom rubber parts with unique properties for your components.
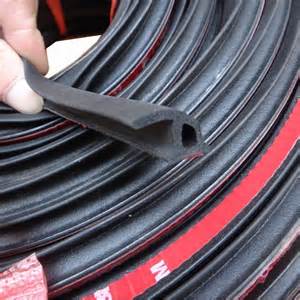
How Are Rubber Extrusions Made?
Custom rubber extrusion products have various uses in the manufacturing, auto and appliance industries, and various other applications. Each extrusion product bears unique characteristics depending on the quality of the rubber and the extrusion process and devices. So how are extrusions made?
What is Rubber Extrusion?
Rubber extrusion and plastic extrusion involve turning rubber compounds into specific shapes for different products and applications. Examples of extrusion products include rubber seals, valves, tubing, vibration reducers, collars, linings, and more.
Extrusion is the process that turns the rubber material fed into the extruder into the final product.
The Extrusion process
There are three main parts to producing rubber extruded products: material, machine, and process. A rubber compound is any raw material fed into a rubber extruder (machine) that heats and pushes it through a die cross-section to achieve the desired product. The final formation usually needs hardening before it’s ready for use in varied applications. Here’s an overview of the extrusion process:
- Rubber Compound Heating
Natural Rubber, EPDM, Viton, Silicone, Neoprene, Nitrile, Butyl, and TPU are the popular rubber compounds used in extrusion. You’ll also encounter SBR, PVC, Provista, Santoprene, Starlink, Synthetic Rubber, and more. Extrusions begin with loading the rubber compound into a feeder hopper and moving it to flutes in a revolving screw. The screws carry the rubber through sections of increasing pressure and temperature, heating and loosening the rubber.
- The Manufacturing Die
Rubber and plastic extrusions come in many shapes, sizes, and dimensions for specific applications in many industries. Since the production is mechanical, it needs a die that shapes the rubber into the desired products. Each product has a unique die, but some dies can extrude more shapes and designs. The increased pressure pushes the rubber into a die located at the end of the extruder. The die receives hot malleable rubber and releases it in specific shapes/products on the other end.
- Mold Vulcanization
Vulcanization refers to hardening the rubber mold/extrusion to form the final product. Extrusions into a manufacturing die are soft and hot, so vulcanization cools and hardens the mold into a safe final product. The term referred to the treatment of natural rubber with sulfur, which is the common practice. However, modern machines accommodate various techniques for hardening different rubber compounds to desired firmness and elasticity.
What to Know About Rubber Extrusion
Rubber extruders result in unique products for specific applications. Each product requires custom vulcanization to achieve the correct firmness or elasticity for the intended purpose. Extruders and manufacturing die also affect the quality of the final product. The rubber compound can swell or shrink during vulcanization, so most tools feature +/- tolerance on the cross-section.
Manufacturers in the auto, motor, solar and appliance industries and anyone seeking custom rubber molds and extrusions need reliable products. Working with experienced and reputable rubber and plastic manufacturers can ensure premium-quality extrusions fit the application. Choosing the suitable rubber compound, die, and extrusion and vulcanization process is crucial.
Quality Custom Rubber Extruded Products
At Clark Rubber and Plastic, we specialize in providing high-quality custom rubber products and extrusions. We’ve got you covered whether you need solid cored extrusions, military-grade profiles, or tubing and sleeves. Our rubber and plastic extrusions serve manufacturers in various industries, and we work with an extensive profile of compounds.
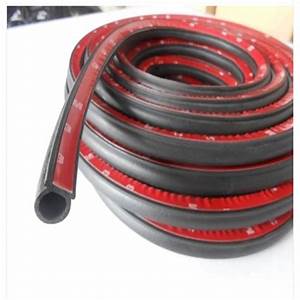
Why Is Injection Molding Used for Plastic?
Are you running a plastic manufacturing company? If so, you must have deep knowledge about plastic injection molding. The process produces volumes of plastic parts for solar, auto, and other related industries.
As the word suggests, the process gets molten plastic injected into a mold. The molten plastic then cools to become solid plastic parts. There is a range of polymers used in injection molding. Among them are nylon, polycarbonates, polyethylene, and liquid silicone rubber.
Reasons Injection Molding is Used for Plastics
Several things make injection molding the best method for plastic manufacturing. Efficiency and reliability are common reasons that make the method great for producing plastic components.
Here are the reasons injection molding is used for plastics.
Efficiency and High Productivity
Efficient manufacturing processes save companies a lot of cash in the end. Injection molding makes plastic manufacturing faster, saving companies time and money. Efficiency also makes it easier for manufacturers to produce a mass of plastic parts and components.
Several things determine the rate of injection molding. One of them is the size of the mold. The smaller the mold, the faster the process, and vice versa.
Another factor is the complexity of the plastic part. The manufacturers use tooling to give plastic parts the right shape and minimize complexity.
For Accuracy
Accuracy is key in the plastic manufacturing process. Injection molding ensures that the dimensions of the manufactured plastic parts and components are consistent. Dimensional consistency aims to create similar end products.
The high pressure during the injection molding also helps create uniform plastic parts. Injection molding makes the manufacturing of complex designs easier. Several factors should be considered to manufacture consistent complex designs.
The first factor is the data collected at the molding center. Comprehensive data collection and analysis are key for accurate and consistent injection molding. Other factors include the training of engineers handling the process and the provided specifications and geometries.
Less Wastage
Low scrap rate also makes injection molding a great method for manufacturing plastics. Computer Numerical Control (CNC) machining and other methods produce more wastage, making them expensive.
Injection molding gets the excess plastics remolded and recycled. Plastic waste is a major threat to the environment. This helps injection molding manufacture plastics while protecting the environment.
To Reduce Labor Costs
Traditional plastic manufacturing is more expensive than injection molding. Automating injection molding eliminates labor expenses, making it affordable for many plastic manufacturers.
Machines and robots in large auto or solar manufacturing companies automate and control injection molding. Streamlining the labor costs makes the entire manufacturing process less costly.
Human errors are common in traditional plastic manufacturing. Mistakes result in defective products, making the manufacturer incur more costs on reworks. Consistency in injection molding eliminates the need for reworks, saving manufacturers good cash.
For Flexibility
There is a range of polymers used in injection molding. You can choose any preferred material/polymer for injection molding. The flexibility aims to manufacture the desired plastic parts and components.
Flexibility comes from the machines used. A good injection molding machine should be able to select the right resins and applications.
The resins should comply with the available laws like Food and Drug Administration (FDA). Other variables that guide the selection of resins are elasticity, water absorption, and tensile strength.
For Durable Products
Injection molding forms strong plastic parts and components. Fillers used in injection molding increase the strength of the manufactured plastics.
Note that the fillers make the plastics strong while minimizing their weight. So, injection molding is the best method for creating quality, portable, and durable plastics. Polycarbonate is the best injection molding polymer for manufacturing strong plastics.
The polymer is strong and resistant to damage. Injection molding is a good method for manufacturing automotive components, eyewear lenses, and containers.
For Multiple Finishes
Injection molding produces plastics with various textures. The surface textures depend on the physical and chemical properties of plastics.
Multiple finishes produced by injection molding prevent the need for secondary applications. Common secondary applications are matter finishes, semi-glass, and shiny plastic finishes. Such secondary applications come with extra costs.
Can Use Many Types of Plastics Simultaneously
Injection molding can use several types of plastics at the same time. Co-injection molding makes it easy for the manufacturer to use different plastics simultaneously.
The ability to use multiple plastics at the same time saves time and increases productivity. Note that the used plastics must be compatible for maximum safety during injection molding. Compatibility also prevents the formation of defective products.
Plastic Injection Molding
Plastic injection molding is a common method used by modern plastic manufacturers across the globe. The method is environmentally-friendly, making it much better than traditional manufacturing. Proper injection molding requires excellent engineering expertise.
Our vision is to excel in modern rubber and plastic manufacturing technologies like injection molding, rubber extrusion, plastic extrusion, die cutting, and more. We manufacture rubber and plastic products used in solar, automotive, and appliances.
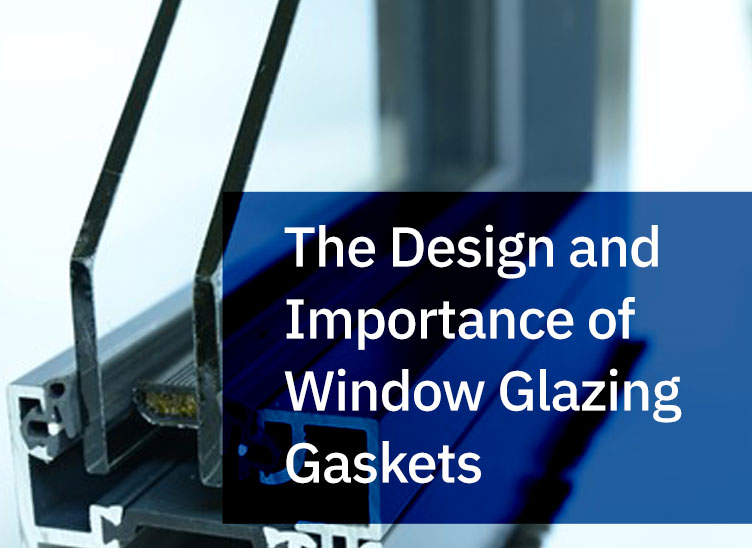
The Design and Importance of Window Glazing Gaskets
Window gaskets are one of those things you don’t miss until it’s gone. They serve an important purpose in cars, windows, solar panels, industrial machines, military equipment, and more. These pieces are made of specially formed rubber materials and installed on stationary edges of glass.
As with most specialized rubber parts, one size does not fit all. There are three important glass measurements that ensure the best fit: the glass thickness, length, and gasket length. There are also foam profiles to consider, such as D-shapes, C-channels, U-channels, and specific forms of glazing seals.
Performance and Energy Efficiency
Using the right glazes and rubber parts is required for performing their base function of shedding and draining water, supporting the pressure points of the glass, and seal against air and water leaks. The main benefit this provides is better performance of glass and increasing energy efficiency.
Whether it is a building, piece of equipment, automotive or aeronautics vehicle, preventing air and water leaks better for proper insulation. This is especially important for thermal insulation in the solar industry.
Preventing leaks is more than just protecting important motorized equipment, though it is that. Leaks increase drag that decreases efficiency in moving parts as well. For military aircrafts and cars, leaking air can create small slow downs that create big impacts.
Proper Production and Installation Processes
Creating the right window glazed gasket means following the right process. Temperature is an important factor in creating the right fit and matching the gasket to its location. Since rubber, metals, and plastics change in heat and cold, it is vital to have materials that perform in the expected temperature ranges.
The best way to prevent major problems is to create shorter pieces and join them with expansion joints. Using a double glazing window gasket when appropriate can also increase the life and performance of window glazing seals.
Using the right materials to seal and install window glazing gaskets is also important. The glazing is an important consideration to optimizing function of the gaskets. Using the right adhesive for the adhesion and sealants, such as wet, dry, or wet to dry is important to preventing gasket failure in the future. Use the best cleaning products to keep the areas free of debris and build up.
It is important to note that deteriorating gaskets are not necessarily a sign that the entire glass unit needs to be replaced. Sometimes the gaskets have had a small leak rom an impact or chip and start to deteriorate. Instead of spending the cost to replace the entire unit, sometimes just the gaskets can be replaced to fix the problem. This option depends on the age and condition of the glass and surrounding materials.
Getting the Right Fit
If you need window glazing gaskets, Clark Rubber and Plastics is equipped to help. We are experts at creating custom rubber extrusion and molding and plastic extrusion products. Send us the measurements for the products you need, and we can create the perfect fit for your project. Contact us today to request a quote for your window glazing gasket needs.
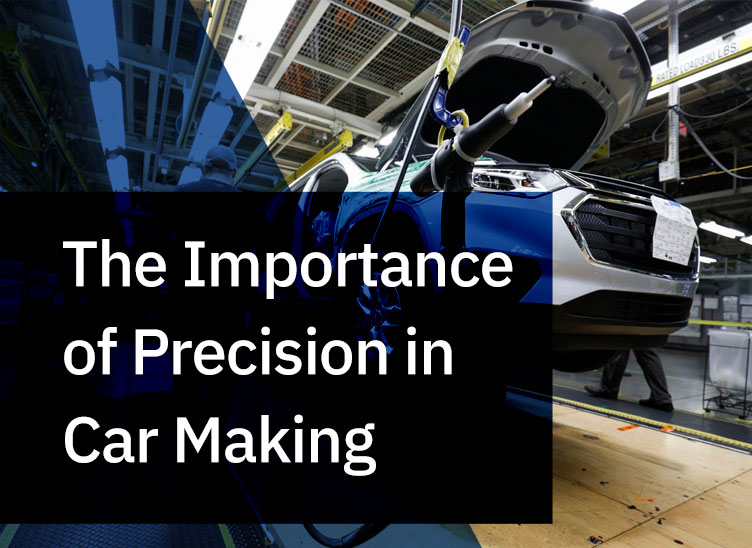
The Importance of Precision in Car Making
Automobile manufacturers have a very serious responsibility. The products they put out on the market can directly impact the safety of the consumer who purchased it.
Of course, every manufacturer has a certain responsibility toward their customers, but this goes beyond slapping a label on the product that says: “Warning, contents are very hot.” If something goes wrong with an automobile they put on the road, it could do no end of harm to the vehicle owner and everyone else who happened to be on the road at the same time.
If a golf club manufacturer creates something that is a few millimeters off spec, this may result in a poor game and a returned club. In a worst-case scenario, there might be a few reviews online about how the manufacturer needs a few more QA checks in place.
Automotive plastic and rubber components do not have any such leeway. Anything less than 100% reliability could, in fact, cost lives.
Precision in every component cannot be overlooked in the automotive industry, which means that all the cutting, milling, molding, and extruding that goes on to produce these parts must be as reliable as everything else in the manufacturing process.
Let’s look closer at some of these processes, what they produce for the automotive industry, and how you know if they are precise enough for your needs.
Precision Die Cutting
Precision die cutting services are a critical for producing reliable gaskets, motor housings, structural components, bumpers, and more. Any automobile on the road today is going to have some very specific tolerance requirements, and every one of these components must meet those demands.
Continuous improvements are necessary to ensure the level of precision required by the automotive industry. This includes finding new ways to perform defect prevention while always minimizing waste.
Precision Injection Molding
The materials used for precision injection molding services are just as important as the tools used to create the final components. Your parts could be made with a wide range of plastics, including HDPE, ABS, nylon, polycarbonate, and a variety of other thermoplastics. Where will they be used in the vehicle? Will they have a direct impact on the safety of the driver and passengers? How much wear will it receive each time the automobile is on the road?
All of these questions have to be answered before the injection molding process can start.
Precision Machining
The sheer number of small and simple – yet extremely important – parts that go into a vehicle means that the manufacturing process will require a cost-effective process to deliver the quality and quantity that is required.
Precision machining plastic parts means that manufacturers can work in small or large volumes, order prototype components when necessary, reduce the costs associated with molds, and get the process started with shorter lead times.
Precision Rubber Molding
A vehicle requires a wide range of rubber parts to increase efficiency and safety. Custom rubber molding services should be able to provide the consistent and precise quality required by the industry standards. Everything from O-rings and seals to gaskets and other components ensure that everything from the transmission and steering to the fuel pumps and AC systems are working properly.
Getting the Essential Components for Every Vehicle
The plastic and rubber components that support the automotive industry keep these vehicles running, the driver’s safe, and the cars looking great. In other words, manufacturers cannot and should not cut corners with any of these parts.
Doors, seats, headlights, bumpers, engine grills, frontend supports, and all the bits and bobs inside every car rely on precise components to perform up to spec. If they are off spec, even a little, then it could cause problems – potentially life-threatening problems – for the person who eventually gets behind the wheel.
So, how can you ensure that you’re going to get the level of precision you need in this industry?
It’s all about finding the right automotive partner.
These types of partnerships have several benefits. Manufacturers can consistently work with people they know – and who share their interest in creating a brand that is known for quality and safety.
Contact Clark Rubber & Plastic today to learn more about our precision services for car making and how our experts can help.
- 1