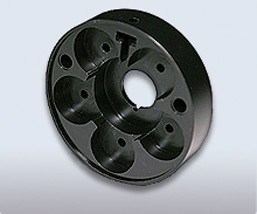
Understanding the Process and Benefits of Rubber Molding
Rubber molding is a manufacturing process used in various industries, including the automotive and appliance sectors. At Clark and Rubber Plastic, our team helps shape materials with precision and high-quality performance. The process delivers reliable solutions to complex manufacturing needs. Here’s more information on the process and benefits of rubber molding:
Rubber Molding
Rubber molding shapes raw rubber materials into desired forms using heat and pressure. The process involves placing an uncured rubber compound into a mold cavity, where it is heated and formed into a product. Different techniques, including compression molding, transfer molding, or injection molding, are involved depending on the requirements of the rubber mold. These requirements could be the design and performance specifications.
At Clark Rubber and Plastic, we specialize in custom rubber molding services, where each product is engineered to meet specific requirements. Whether it’s a small, intricate component for appliances or a large, durable part for military defense systems. Custom molding will make sure the material, tolerance, and mechanical properties align with the project’s goal.
Molding Across Industries
A broad range of markets uses tailored molding solutions to meet industry performance standards, including the automotive industry. Molded parts are key for vibration dampening, sealing, and protecting key components. High-performance rubber products can withstand vehicle conditions, including under-hood temperatures and exposure to oil and chemicals. These products help enhance safety, durability, and efficiency. Here are some other industries that utilize the molding process:
Appliance Industry
Rubber molded components can provide insulation and cushioning for a variety of products. This includes washers, dryers, and refrigerators. Rubber components are precision-molded to integrate seamlessly into appliance designs. They can maintain compliance with durability and safety requirements.
Military and Defense
Molded parts in this field must meet strict specifications and operate effectively in various harsh climates. Molding processes help to create reliable solutions that support mission-critical operations. Some parts produced include various armaments and munitions, insulation for engine compartments, and marine vessel applications.
Benefits of Custom Molding
Some advantages of using custom molding include accurate tolerances and shaping. Rubber molds can be customized to form unique components. At Clark and Rubber Plastic, we use a variety of materials and compounds to meet chemical resistance, flexibility, hardness, and environmental performance. We make sure parts can withstand stress and require reduced maintenance.
Our team will review simple and complex part geometries, supporting innovation in product design. From small prototypes to large-scale production, our team can meet the manufacturing needs of projects of various sizes. Molded parts are inspected to make sure they meet industry standards.
Use Clark and Rubber Plastic for Molding
Understanding the process and benefits of molding is key to product performance and reliability. Our Clark and Rubber Plastic team provides end-to-end support, from design consultation and prototyping to production and delivery. If you’re looking for reliable custom rubber molding services, our team can provide support using multiple materials. Contact our team today to learn more about our rubber molding processes and how we can customize your solution for various parts.
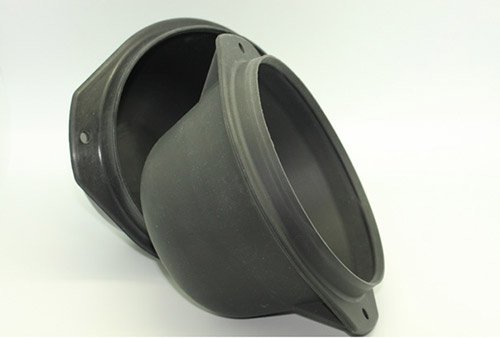
How To Choose a Suitable Rubber Molding Process
Choosing a suitable rubber molding process can improve the quality and performance of a product. Clark Rubber & Plastic helps clients choose a rubber molding process that will promote the integrity of their products. Here are some tips for choosing the proper molding process.
Understand Your Project Requirements
Defining your project’s needs can help you choose the right rubber molding process. Projects may vary in complexity, volume, or material specifications, necessitating different production methods. If you need parts with tight tolerances, injection molding may be the most suitable option. Compression molding may be the right choice if you need large, simple parts. At Clark Rubber & Plastic, our expertswill analyze your project requirements and goals to recommend a process that will help you achieve your desired results.
Evaluate Different Molding Processes
Some of the top rubber molding processes include injection, compression, and transfer molding. Injection molding helps manufacturers produce large quantities of products with complex parts and tight tolerances. Compression molding is suitable for creating large parts and lower production volumes. These characteristics make compression molding a more cost-effective and versatile option for some industries.
Transfer molding combines injection molding and compression molding. This results in a balance of precision production and cost-effectiveness. Some rubber materials may be better suited for specific molding processes. Clark Rubber & Plastic’s team understands each material type and molding process, allowing us to recommend the right process and material for your needs. Our facility also has advanced injection presses that can handle projects of various sizes.
Determine Material Requirements
The type of rubber material that you select impacts the performance of your final product. Clark Rubber & Plastic offers a variety of rubber materials, like natural rubber, neoprene, nitrile, and EPDM. Natural rubber is elastic and durable. This makes it an ideal choice for components used by automotive industries. Neoprene is resistant to oil, chemicals, and weathering. These characteristics make neoprene suitable for products intended for outdoor use. Nitrile is resistant to oils and fuels, so it can be used for parts in the automotive and aerospace industries that are exposed to oil and fuel. Dense and foam forms of EPDM work for weather-resistant applications, like gaskets and seals. Our team helps clients confirm that their material selection and final product will meet their industry’s quality and safety requirements.
Prioritize Prototyping and Testing
Prototyping and testing your products before production can help confirm that your chosen molding method meets your project specifications and performance requirements. Refining your prototype allows you to identify and remove design flaws and try more efficient molding techniques. Clark Rubber & Plastic offers prototyping services to help clients design and produce effective products.
Partner With a Rubber Molding Manufacturer
Choosing a suitable rubber molding process can enhance your product’s quality and help you stay within your manufacturing budget. Partnering with an experienced manufacturer helps you achieve desired results with less trial and error. Clark Rubber & Plastic offers high-quality, custom rubber molding services and raw materials for small-batch and large-production projects. Contact Clark Rubber & Plastic today to learn more about how we can partner with you for your next project.
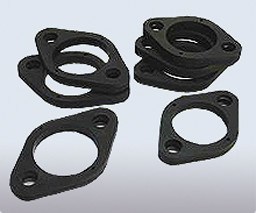
6 Tips for Working With a Rubber Molding Manufacturer
Working with a rubber manufacturer requires an understanding of their production processes and different specifications. After a good relationship has been established, you can receive products of consistent quality and have access to efficient manufacturing solutions at Clark Rubber and Plastic. Outlining project specifications, choosing the proper molding process, prioritizing quality control, and more will help to make the process more streamlined. Here are six tips for working with a rubber molding manufacturer:
Outline and Define Project Specifications
Having a clear outline of your project’s requirements will help to prevent any miscommunication and delays. Including part dimensions and the volume of parts you need in your outline will help the rubber molding manufacturer meet your production goals. Selecting the right material for the part’s purpose should also be considered because incorrect material may lead to performance issues. Other factors to keep in mind include tensile strength and temperature resistance.
Choose the Appropriate Molding Process
Different molding processes impact a part’s cost, production lead time, and overall performance. Compression molding works for smaller production runs and simpler parts. For parts with more intricate designs, transfer molding may be an appropriate choice. Injection molding is often preferred for its repeatability if you want to create large batches of parts. The manufacturers at Clark Rubber and Plastic can help you determine the optimal process for your project, as each method has different material requirements.
Look Into Quality Control
Defects throughout the manufacturing process can increase your costs and missed deadlines. Professional manufacturers have rigid quality assurance protocols to mitigate these risks. Check to see if they conduct material testing to verify that the quality of their materials meets industry standards. You can also work with a manufacturer that provides prototypes, allowing you to inspect the product before a full-scale run.
Understand Manufacturing Tooling
An understanding of tooling when working with a manufacturer is helpful because it affects costs and production quality. Two factors that influence tooling choices are the complexity of the desired part and the material it will be made from. Soft and hard tooling are the two most common types, and deciding which to use depends on the material used, its durability, and the application of the product. Choose to work with a manufacturer that offers a wide range of tooling options to meet your specific production requirements.
Plan for Rubber Molding Lead Times
A variety of factors influence product timelines, such as material availability, mold creation, and manufacturing capacity. Additional sourcing time may be necessary for specialty materials. Mold fabrication times can vary depending on the complexity of the mold. Each molding process used by Clark Rubber and Plastic also comes with its own manufacturing capacities. Injection molding works well for high-scale production runs, while compression molding creates smaller batches and will take longer to meet specific demands.
Compare Costs and Values
Choose to work with a manufacturer that operates both efficiently and produces high-quality products. Efficient use of materials creates less waste and lowers the costs associated with production. Quality components may cost more, but they tend to reduce failure rates and the need for replacement costs in the long term.
Choose Our Molding Operations
Working with the right rubber molding manufacturer will help you create reliable parts that provide lasting results. Streamline the manufacturing process by outlining your production needs and communicating them to the manufacturer. Contact Clark Rubber and Plastic today to learn about our molding services.
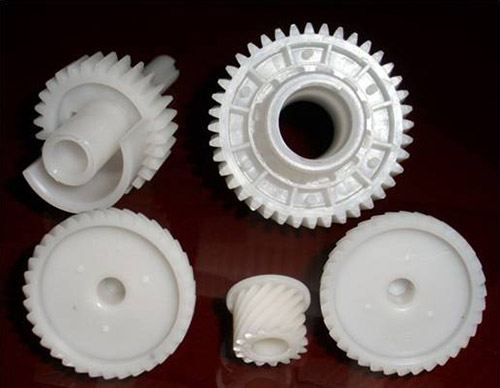
Three Questions To Ask Your Rubber and Plastic Manufacturer
A rubber or plastic manufacturer can help you create a high-quality custom rubber or plastic product. Services at Clark Rubber and Plastic include custom plastic and rubber molding. Here are three questions to ask your manufacturer:
1. What Are Your Capabilities and Services?
When deciding on a manufacturer for your product, make sure that they offer the production services you require for your project. Ask them about their plastic and rubber molding capabilities, as well as extrusion services. Clark Rubber and Plastic provides precision die-cutting to meet product specifications. Our plastic and rubber extrusion processes offer a wide variety of textures and thicknesses, and our custom plastic injection and rubber molding process allows us to create custom parts and products.
See if your manufacturer offers additional services, such as milling and packaging. This allows you to work with one manufacturer for your product instead of multiple suppliers, simplifying the process and reducing production time. We offer digital printing and milling at Clark Rubber and Plastic. Our taping services include heat-activated tape services for packaging and product needs.
2. What Kind of Product Runs Do You Offer?
Check with the manufacturer to see what their volume capabilities are. Ask about:
- Prototype production: If you are making a prototype for your product, ask your manufacturer to see if they offer low-volume services.
- Size of the facilities: For a longer product run, see if the facility has the equipment and the space to undertake larger projects successfully.
- Production rate and times: Check to see if the projected production rates, turnaround, and lead times fit with your project schedule.
Our 40,000-square-foot plastic operations facility and our high-quality equipment and tools at Clark Rubber and Plastic enable us to offer both long and short product runs. Our computer numerical control processes allow us to provide fine details and high levels of accuracy for products of all sizes. We can take on projects of various complexities and sizes. We also help you stay on schedule with a faster turnaround time.
3. What Quality Standards Do You Follow?
Make sure the manufacturer you are working with can meet your industry’s product standards. Depending on industry requirements, plastic and rubber products should be able to withstand:
- High temperatures
- Constant use
- Extreme weather conditions
We are dedicated to providing high-quality plastic and rubber extrusion products. Clark Rubber and Plastic has developed a quality control system that we follow to make sure that all our products meet high production standards and safety requirements. We utilize certified high-quality materials for our components and products to provide structural integrity and durability.
Contact a Plastic and Rubber Molding Manufacturer
The industries we provide products for include the automotive, appliance, consumer, military, and solar industries. We utilize precision machinery, and we can also work with metals, such as steel. You can request a quote for our plastic and rubber molding and other available services through our online form. If you are interested in partnering with Clark Rubber and Plastic, we invite you to call or email us today.
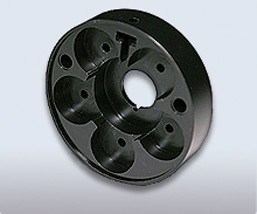
How To Choose a Rubber Manufacturer for Your Molded Products
A variety of industries use rubber to build solar panels, automotive parts, or medical devices. The right rubber manufacturer will use high-quality materials to deliver prototypes or full production services. Here is some more information on how to choose a rubber molding manufacturer for your business:
Request Quotes
Quotes are useful for businesses looking to partner with a rubber manufacturer by receiving valuable information on a variety of our services. They allow you to compare market rates and budgeting requirements, as well as request material samples from us. Your business will then be able to submit an order form, which begins the process of production. If you need a prototype, we will complete that step first for final approval before fabricating larger quantities.
Some of the applications we provide include custom rubber molding services, die cutting, and plastic extrusions. If you need a service that is not currently listed on our quote form, provide a short description in the “other” box. Additional details like material requirements and production deadlines are beneficial for us to know to meet your fabrication expectations.
Review Materials List
Professional rubber molding manufacturers provide a list of material options to meet your production goals. Some materials include silicone, neoprene, and natural rubber. Each product is inspected for quality assurance to meet specification requirements and industry standards. Our certifications include the American Society for Testing and Materials (ASTM) and the Rubber Manufacturers Association (RMA). If you’re unsure about what kind of material your product should be fabricated from, our team will provide professional guidance and samples.
Look For Responsive Customer Service
A benefit of partnering with us is our responsive customer service team. Our service members establish open communication pathways via email to keep you informed about the progression of your order. They are also available to assist you with submitting orders, uploading file formats, and making any necessary changes to your prototypes. Transparency is beneficial for companies looking to make long-term partnerships with us, as it allows for mutual trust and professionalism.
Check Production Capacity
Look for a manufacturing company that is capable of producing a range of quantities for your business. Small batches of product are useful for those with growing businesses, while large-scale production is beneficial for distributors that provide services across the country. These flexible options allow your business to order for restocks, new projects, or to create prototypes for investors.
Production timeframes vary depending on the quantity of products and what type of application they’re made with. Certain applications like custom molding may extend the timeframe for fabricating your product. Custom die cutting may also take longer to set up, as each machine must be fitted with the correct die. You can check the progress of your order by contacting us via telephone or email.
Contact a Rubber Molding Manufacturer
At Clark Rubber and Plastic, we provide manufacturing solutions for a range of industries and applications, including home construction and renewable energy products. Our production line is capable of handling small batches or full production quantities. Custom molding is also available for those looking to expand their current inventory. Contact us today by email or submit a quote form to learn more about our services.

7 Industries That Use Plastic and Rubber Molding Services
Plastic and rubber molding services play a key role in many manufacturing processes for various industries. Each industry depends on materials made from molding processes to increase the functionality of its products. At Clark Rubber and Plastic, we manufacture high-quality materials that meet our clients’ demands. Here are seven industries that use molding services:
1. Automotive
The automotive industry uses plastic- and rubber-molded products to produce components that enhance a vehicle’s safety, performance, and comfort. These products include tires and seals to prevent flat tires while driving. Interior and exterior elements include bumpers, door panels, and interior trims. Engine parts like hoses, belts, and mounts support the engine and are heat resistant. Manufacturers also use rubber and plastic moldings for electrical wiring coverings.
2. Healthcare and Medical Equipment
Healthcare industries rely on rubber and plastic molding products to produce safe, sterile components for patient care and medical advancements. These include medical devices such as ventilators, blood pressure monitors, and diagnostic equipment. Other products, such as surgical instruments, use rubber for sterile solutions. Manufacturers use custom-molded materials to make lightweight prosthetic and orthotic devices.
3. Consumer Goods
Rubber molded products are designed for everyday household items, such as kitchen utensils and tools like silicone baking molds. Many toys are rubber-molded to make sure they are child- or user-friendly. Soles and inserts in footwear are often molded from rubber to be slip-resistant while providing comfort. Other household moldings contribute to personal care products and their ergonomic design.
4. Electronics and Electrical
Plastic and rubber molding services create protective coverings for wires to resist environmental factors like heat and moisture. Plastic moldings are also used to make connectors, sockets, and plugs to house wiring connections and prevent the wires from touching. This can prevent sparks. Household electronic devices contain lightweight molded pieces to protect components from dust, water, and other contaminants.
5. Construction and Infrastructure
In construction, piping and fittings use rubber gaskets to seal plumbing and water management systems. Rubber molding services also create seals for windows, doors, and HVAC systems for weatherproofing and maintaining energy efficiency. Plastic and rubber are necessary to produce personal protection gear such as safety boots, gloves, and eyewear.
6. Renewable Energy
Engineers use molded rubber seals in dams and turbines to make sure they are water-tight. Rubber hoses are utilized because they can withstand extreme temperatures and pressures. Plastic framing protects solar panels from environmental conditions.
7. Aerospace
Components on aircraft, such as shock absorbers and fuel system parts, are from rubber molding services. Even items inside the aircraft, like tray tables and door handles, are built from moldings. These parts are durable enough to withstand changes in air pressure during take-off and landing.
Schedule Rubber Molding Services Today
Plastic and rubber molding services are used in industries worldwide, offering durable and lightweight materials. Our rubber molds support natural rubber, neoprene, and nitrile. From vehicle safety and medical equipment to everyday household products, molding services are integral to manufacturing. At Clark Rubber and Plastic, we deliver top-quality molding services to fit your needs. Call us today to schedule production for your next project.
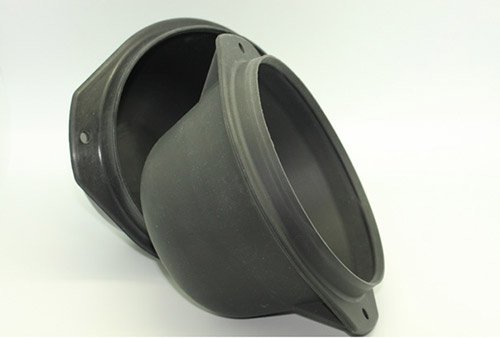
The Rubber Overmolding Process and Why It’s Used
Rubber overmolding is used in a variety of industries, including appliance, automotive, solar, and military. In rubber molding, plastic or other materials are encased in a layer of rubber molding to become a single custom part. Clark Rubber and Plastic provides this and other types of rubber processing for your needs. Here is the rubber overmolding process and why it is used:
What Is Rubber Overmolding?
Rubber overmolding is the process of pouring rubber over existing parts or into a mold to create a new item. This may include cell phone cases, toothbrushes, electronic parts, and more. After a hard substrate, like plastic or metal, has been molded to the desired shape, rubber is injected into the mold to cover the substrate. Rubber may also be poured into a mold without a substrate. We provide molding services for natural rubber, neoprene, nitrile, silicone, and more. Overmolding can also create parts with tight tolerances to make sure all elements fit together precisely.
Why Is It Used?
Rubber molding is used to improve a part’s longevity or to add cushion between parts or on tool handles. At Clark Rubber and Plastic, we offer consultations to determine your project goals and recommend the best molding process. Here are some reasons we may recommend overmolding:
Improved Grip
Rubber provides a natural grip when applied to items. The handles of tools like screwdrivers, wrenches, and hammers are often coated in rubber to offer additional grip or prevent the tools from slipping out of your hand during use. The medical industry also uses this process for tools like syringes, catheters, and dilators to reduce injury during surgery. Car part manufacturers also use this type of molding to protect parts from damage.
Shock and Sound Absorption
Overmolding helps absorb shock, which is beneficial in motor vehicles. During a collision, rubber helps absorb the impact, reducing the damage to your car. Stereos can also be protected from shock and sound damage by using overmolding on their components. We provide a variety of rubber moldings to protect your inventory from damage. Rubber mats can be added to workshops or other facilities to reduce noise and floor damage from vibrating machinery.
Improved Durability
Overmolding helps make items more durable. Applying rubber over the substrate helps preserve the tool’s base components, prolonging its life. Rubber can stretch and move, helping prevent breakage when heavy items are dropped or are in constant motion. For better protection, use rubber molding on parts that are frequently used and impacted.
Waterproofing Seal
Use overmolding where parts join to create a waterproof seal. Rubber is vulcanized with oxides and sulfur, so it is denser, and water rolls off. This is ideal for motorized vehicles, pumps, roofs, and other applications. Shoes use rubber to keep feet dry and protect them from impact with each step. Many rubbers are also resistant to gas and steam, helping to contain liquids within product parts like piping or storage tanks.
Rubber Molding for Your Business
Rubber molding and overmolding can help your business protect the key components and tools for your equipment and manufacturing projects. They provide shock and sound absorption, waterproofing, and gripping qualities that help enhance the durability of your items. The molding facilities at Clark Rubber and Plastic use advanced equipment to deliver high-quality products in low—or high-production quantities according to your deadlines. We also offer printing, assembly, packaging, and kitting services so your product is ready for use or shipping. Contact us today, and we can help you create the parts and molds you need.
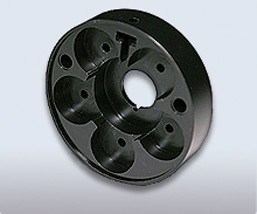
What Materials Are Used in Rubber Molding?
Rubber molding services are a good solution for businesses that need custom parts for various applications. At Clark Rubber and Plastic, we produce customized rubber components that match the dimensions and production value of each project. To create these products, we use materials like natural rubber, neoprene, and nitrile. Here’s more information about the molding process and the materials and equipment we use:
Rubber Molding Process
Rubber molding is the process of turning raw materials into unique shapes that serve a functional purpose in many applications. Manufacturers in the automotive, solar, and home appliance industries use rubber parts as seals, gaskets, tubing, and anti-vibration pads. The molding process begins by selecting a rubber type and adding it to a high-heat chamber. In this chamber, the rubber melts to become more pliable. Once the melted rubber has an even consistency, it enters a mold or die, where it is formed into a unique shape. After the molded rubber cools, manufacturers cut it to size to match the project’s requirements. The final rubber components are then ready to be shipped to the customer.
Rubber Types
Depending on the specifications of your project, you can choose from uncured rubber materials like natural, liquid silicone, ethylene propylene diene monomer (EPDM), nitrile, and neoprene rubber. Some rubber types, like EPDM and neoprene, are more resistant to heat and chemicals. These characteristics make the material ideal for creating components that will be used in engines and environments exposed to extreme weather. Natural rubber has significant rebound resilience and flexibility, making it useful for products like seals and gaskets. If you are unsure which rubber is most suitable for your project, our team will recommend rubber types that will resist damage, offer flexibility, and remain durable over time.
Colorants
To create a fully customized rubber product, you can select a colorant. Manufacturers add the colorant to the prepared rubber before heating it to confirm the materials melt and combine evenly. This process results in a solid-colored rubber product that matches your business’s branding or the intended application.
Melting Chambers
After combining colorants and uncured rubber materials, manufacturers pour the mixture into a hopper that leads to the heating chamber. While in the chamber, the materials are heated until they melt and are ready to be placed into the mold. These machines may have dryer components that keep moisture away from the rubber as it melts, preventing contamination.
Molds
Rubber molds are typically made from metal materials to confirm the melted rubber is held firmly in place as it cools. Some molding methods include injection, compression, and transfer. Our team will recommend a molding process that matches your product type to make the production as efficient as possible. The mold may be designed to produce a single part or multiple components at once, with specific dimensions for each project.
Explore Rubber Molding Services
Clark Rubber and Plastic offers molding services to companies in various industries. We use computer numeric control equipment to make sure your products are as precise as possible. This equipment also allows us to produce a high volume of rubber components in a short amount of time. Contact our team today to learn more about our molding processes for rubber and plastic parts.
- 1